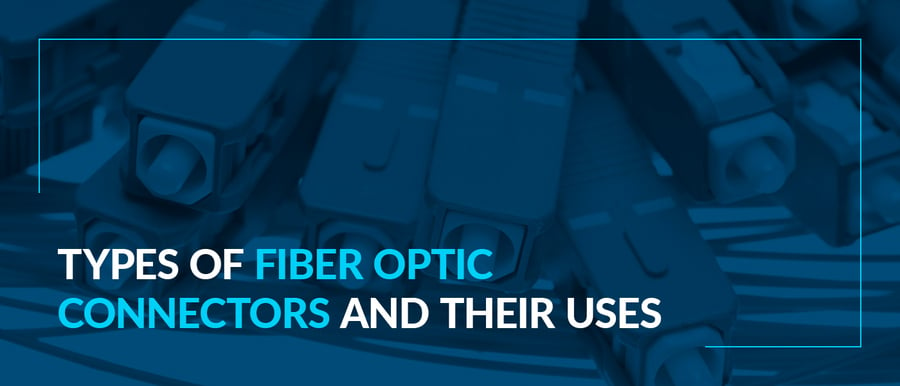
Connectors, also called terminations, link
cables together with a secure connection that permits pulses to travel
through the cable without interruption. To accommodate different
applications, there are many fiber optic connector types. Choosing
between the correct connector types for specific use ensures ideal
performance of the fiber optics cables and the devices they connect.
What Is a Fiber Optic Connector?
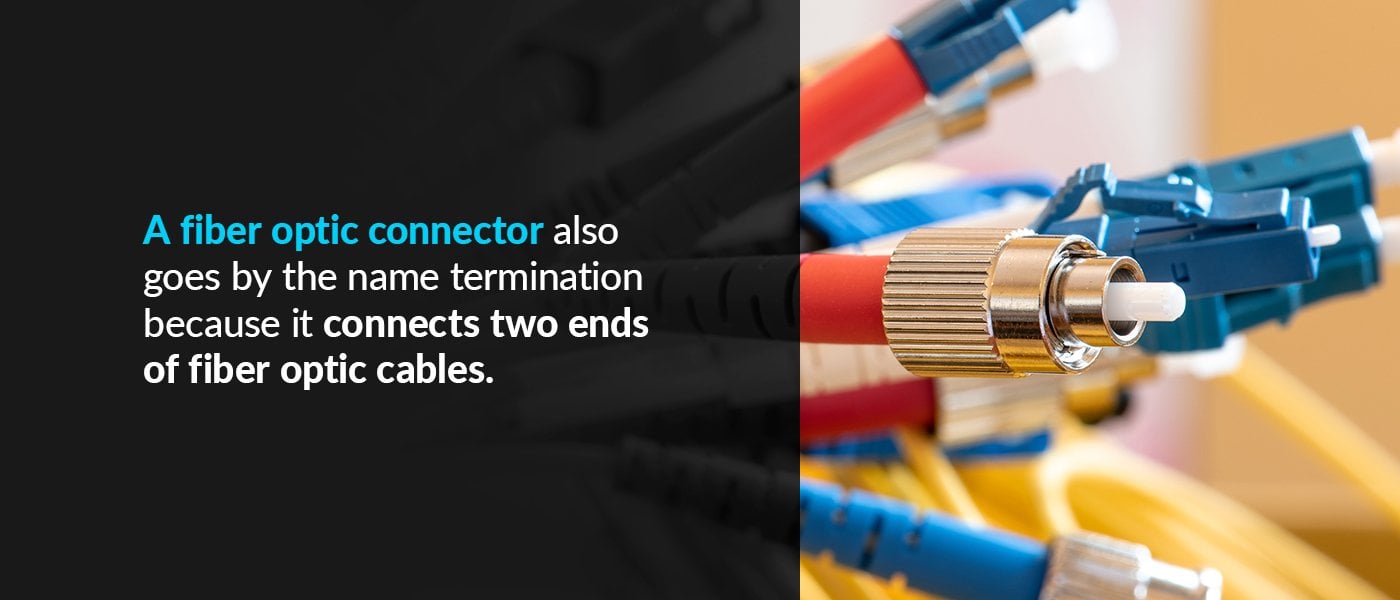
A fiber optic connector also goes by the name termination because it
connects two ends of fiber optic cables. These connectors hold the fiber
optic cables together inside the ferrule to attach them to the other
side of the cables. Ferrules are the connector end pieces that include
the method of connecting and securing the termination. Some ferrules
will plug into a mating adapter and screw to hold the two portions
together. Others use a bayonet design, while some snap together.
Some ferrules have a spring-loaded
connector to hold the pieces together with constant force for improved
connection. Most fiber optic connectors require effort to connect and
disconnect, reducing the chances of accidentally pulling the cables
apart during typical use or installation of other components. Connectors
can also bring a cable into a converter or directly into the device
serviced by the fiber optic cable.
What Are Fiber Optic Connectors Used For?
Terminations have multiple uses, depending on the fiber optic cable connector types used. For instance, fiber optics have uses in the following areas:
1. Internet and Local Area Networks (LANs)
Fiber optic cables allow for greater
bandwidth compared to other cable options. Common uses for networking
include fiber optics for delivering internet and LAN connectivity
throughout a building. Fiber optic cable works especially well over
distances greater than 90 meters and when carrying gigabit-speed connections. Both LAN and high-speed internet use multimode fiber optic cable.
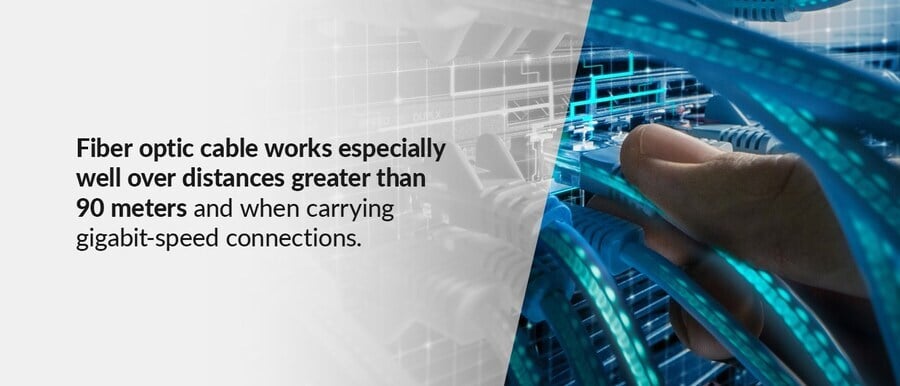
Many companies today have fiber cable going to telecom closets that
then transfer the signal to copper-based Cat5 cable and other cables.
These cables carry the signal to computers and telephones. However, this
practice of using media converters or telecom closets may disappear
over time. Innovations in fiber optic technology, high costs for
maintaining telecom closets and lowering prices for fiber optics may
eventually make all fiber networks the norm.
2. Community Antenna TV (CATV) and Other Telecommunications
Community antenna TV and other
telecommunications companies often prefer fiber optic cable to deliver
their signals due to the lower cost over long distances with less loss
and higher bandwidth compared to older technologies. Additionally, each
transmitter and receiver pair of fibers can carry more voice and video
signals. Compared to wire delivery methods, fiber optics can go 100
times farther and more than 1,000 times faster. CATV may use single-mode
fiber optic cabling for its higher bandwidth and lower loss.
3. Digital Telephone Service
Telephony is another system that benefits
from fiber optic cable use. Like CATV, many digital telephone
applications use single-mode fiber cable. In fact, in the business
world, telephony is one of the top uses for fiber optic cables.
4. Public Utility Networks
Public utilities, such as electrical
companies or municipal water treatment facilities, use fiber optics in
several ways. They may have fiber optic connected closed-circuit TV
(CCTV) security cameras and a network connecting various sites to
provide real-time data on operations. Electrical companies, for
instance, recognized the interference of their production and
distribution equipment on traditional communications wires and made an
early switch to fiber optics.
City emergency services also use fiber
optics with CCTV, wireless technology and traffic cameras to integrate
communications and information sharing among responders. Plus, fiber
connectivity through in-city networks can offer higher bandwidth to
accommodate large numbers of city workers on the system accessing
information at once.
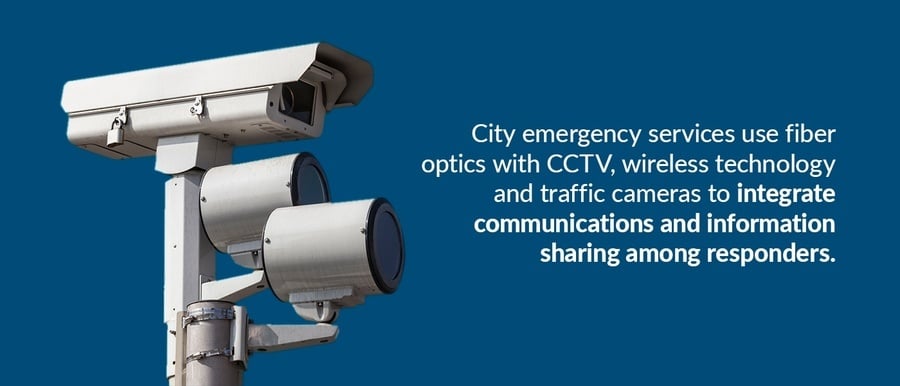
5. Industrial Networking
As with electricity companies,
electromagnetic interference also plays a role in the choice of
communication products used in industrial businesses. Electrical noise
from equipment can cause severe problems with unshielded wire cable. But
it does not do the same for fiber optics. With many industrial
facilities moving into smart operations with devices connected to each
other and the internet over a network, reliable connectivity is vital.
For industrial applications, connectors
must have firm attachments that cannot easily dislodge, even from
constant vibrations caused by machinery operating nearby.
6. Military Networks
Military operations need connectivity in
some of the harshest environments on the planet. Battlefields, naval
ships, military bases and planes all need to have means of connecting.
Interference, movement and tapping into the communications lines pose
threats for the military. Fiber optic cable resolves these issues. Plus,
on vehicles and planes, it reduces the weight required for
communications hardware.
7. Security Systems
Security systems often need reliable data
transmission lines that can deliver video and audio quickly. Fiber optic
cabling for closed-circuit TV (CCTV) offers multiple advantages. First,
the two-way direction of fiber optic cable allows an operator to
control the camera angle when needed. The ability to control the camera
ensures better viewing of suspicious targets, which improves security.
The high bandwidth of fiber optics permits
multiple cameras to transfer signals over a single cable. Additionally,
fiber optic cable can stretch out over long distances with minimal loss.
Therefore, securing cities, airports, warehouses, factories and other
larger facilities is possible thanks to fiber-optic connected CCTV. CCTV
is not the only security system use for fiber optics, though. Some
systems can use sensors and perimeter alarms connected through fiber
cable for a comprehensive means of monitoring a property's security.
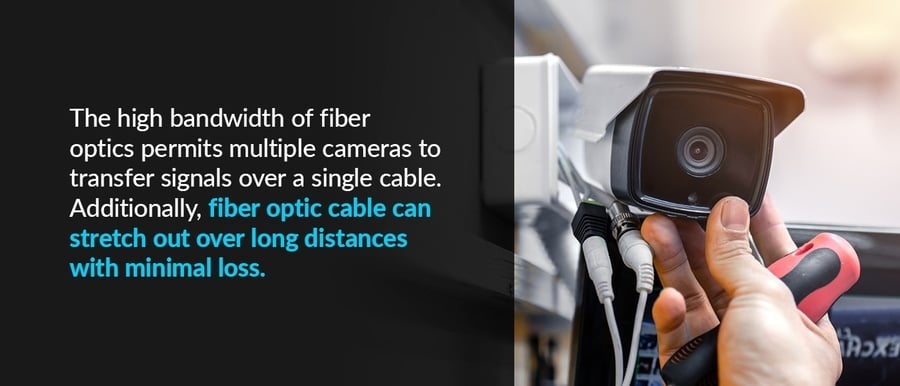
8. Lighting
One of the least considered applications of
fiber optics is the ability to transfer light over long distances
rather than data signals. Therefore, lighting heat-sensitive locations,
difficult to reach places or sites where standard electric wiring could
be dangerous can use fiber optic lighting. Some common uses of this
type of lighting include museum displays near delicate artifacts and in
fountains or swimming pools. With multiple filters and the ability to
automatically switch them, color-changing effects are possible.
What Are the Types of Fiber Optic Connectors?
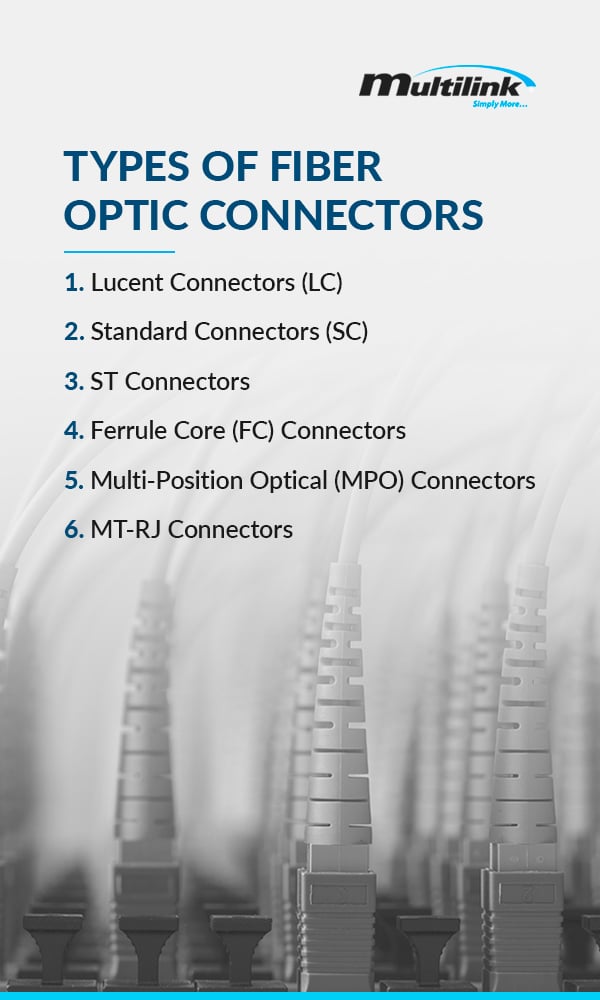
Fiber connectors differ based on what types
of cables they connect. For example, single-mode fiber connectors and
multimode fiber connectors each pair with the cable with the same mode
compatibility.
With many electronics that require fiber optic connections, several types of terminations exist. The most common fiber connectors are LC and SC. SC
and LC connector types are so common that many systems have designs to
accommodate them. What are the different types of fiber connectors? They
are as follows:
1. Lucent Connectors (LC)
LC connectors have some of the smallest
ferrules, measuring 1 1/4 mm, which is approximately half the size of an
ST connector. Their tiny size puts them into the small form factor
category of terminations. These connectors work well for multimode
transceivers and single-mode cables.
2. Standard Connectors (SC)
SC connectors have a 2 1/2 mm ferrule that
snaps cleanly into place. Using a push and pull motion secures the
connector. These types of terminations have high levels of performance,
which along with a price drop since their introduction, has contributed
to their vast popularity in multiple applications. In fact, many
formerly ST connectors applications now use SC connectors instead, since
SC was invented to supplant ST in both telecommunications and data
communications.
3. ST Connectors
ST connectors are among the oldest of fiber cable connector types. Until 2005, this proprietary AT&T brand of connector ranked
as one of the most popular fiber terminations. While solutions that
solve some issues ST connectors present have replaced these connectors,
they still remain popular. Today, their cost is low due to their age,
making them a choice for budget-mindful projects.
The design of ST connectors is a 2 1/2 mm
ferrule that has a bayonet-style connection between the fibers through
an adapter. These ferrules use a spring-load design that can make
installation difficult unless the parts have precise seating, though a
keyed slot assists with aligning the ferrules for connection.
4. Ferrule Core (FC) Connectors
FC connectors rank as some of the most
popular for use with single-mode connections before the introduction of
LC and SC connectors. These use a keyed, screw-in type ferrule. However,
the process of screwing in the ferrule requires extra time and effort
compared to snap-in SC connectors.
The screw-in design prevents the connection
from interruptions, even when someone pulls the cable or the system has
applications in areas with a lot of movement. Video over fiber is one
use for these types of connectors due to the constant flow of data
through the cable and the security of the connector.
Like ST and SC connectors, FC terminations
use a 2 1/2 mm ferrule. With a hybrid adapter, anyone can create a
bridge between these connector types.
5. Multi-Position Optical (MPO) Connectors
MTP is the commercial brand of MPO
connectors. MTP and MPO connectors are the same, except the MTP brand
has a specific use for high-performance applications, whereas MPO works
on more mechanical situations. These two connectors usually connect
ribbon cables with multiple fibers.
These connectors have two to six rows of 12
or 16 fibers. MPO connectors with 12 fibers per row can have two to six
rows, with two the most common number. Connectors that have 16 fibers
per row do not have more than two rows. Connections between ferrules use
pins and holes to mate the ends of the fiber with another cable or an
electronic device. Most often, this type of connector has applications
in either high-speed links that use multimode or for pre-terminated
cable groupings.
6. MT-RJ Connectors
Today, MT-RJ connectors have disappeared
from use. However, some systems may still require these connectors for
repairs. MT-RJ only works for multimode cables with duplex fibers. Both
fibers go into the ferrule that connects to its mated half with pins and
holes, similar to MPO terminations. Some plug-and-jack variations on
this type of connector also exist.
What Are the Advantages and Disadvantages of Fiber Connectors?
Fiber connectors have distinctive pros and
cons for the different models. When considering the different types of
connectors, weigh their applications and the positive and negative
attributes of each to ensure proper selection and installation of the
terminations.
Advantages and Disadvantages of LC Connectors
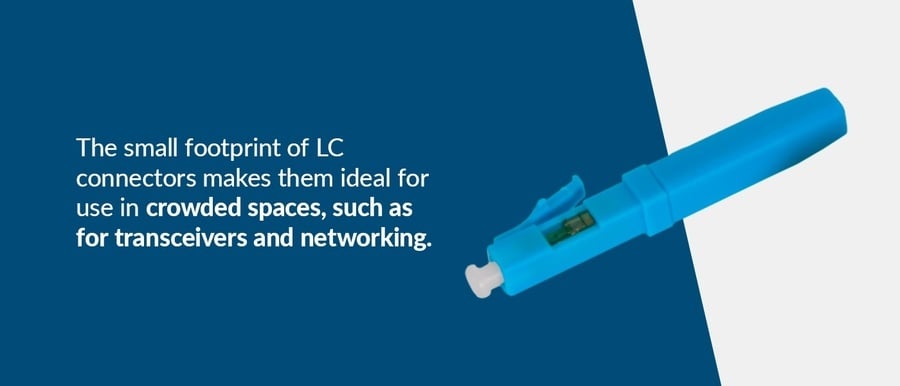
The small footprint of LC connectors makes
them ideal for use in crowded spaces, such as for transceivers and
networking. Other advantages of these terminations include the ability
to use a clip to convert to a duplex from a simplex and the ease of
adding a connector to the end of a cable. These connectors also have a
design that makes pulling them out of place difficult.
The small size can pose a problem when
removing them, especially in high-density sites. Most people have
difficulty reaching the clip to disconnect these terminations due to the
tiny size of the ferrule and the cramped space these connectors often
appear in. Many people solve this issue by using an extractor for LC
connectors.
Advantages and Disadvantages of SC Connectors
SC connectors have a square shape for the
ferrule, which eases arranging them into a small space. Plus, its sturdy
hold prevents connection problems, even if someone pulls the cable.
This advantage solves an issue with ST connectors that can interrupt
fiber optic signals if someone pulls on the cable. Since the SC has a
standard 2 1/2 mm size, it can pair with an FC or ST connector with a
hybrid adapter.
The disadvantage of using SC connectors is
the size of their ferrules. These connectors require more space than
small form factor designs, like the LC. Therefore, for the most compact
spaces or crowded areas, LC connectors might provide a better solution.
Advantages and Disadvantages of ST Connectors
Since ST connectors are older, several
multimode fiber cable systems use these types of terminations. While
pushing and twisting each spring-loaded ferrule is simple, the process
does require more time than other connectors. In some instances, the
spring-loaded connector can disrupt the connection by pushing the fibers
together when someone pulls the cable.
When working in small spaces, pushing in
and twisting each connector also becomes difficult, especially in cases
when the two halves do not have proper seating for a solid connection.
Disadvantages and Advantages of FC Connectors
FC connectors work in situations that may
require assurance of a termination that will interrupt data flow. For
applications such as industrial environments or on ships that may
encounter rough conditions and cable movement, FC connectors work well.
Since these connectors screw into place,
they also need more time for installation. In densely packed spaces, the
round shape and screw-in connection require more space for installation
and stacking compared to square-shaped SC connectors.
Pros and Cons of MTP and MPO Connectors
The ability to bundle multiple fibers onto a
single connector is the biggest advantage of MPO connectors. When used
in high-density situations, MPO connectors can save space compared to SC
connectors or other alternatives. Another advantage of some MTP
connectors is the ability to remove the exterior housing to easily
change the type of connector or repolish the ends.
While MPO connectors offer many advantages
over other terminations, especially in crowded racks, this feature also
is a drawback. With so many fibers housed in a single connector,
cleaning the connectors efficiently is difficult.
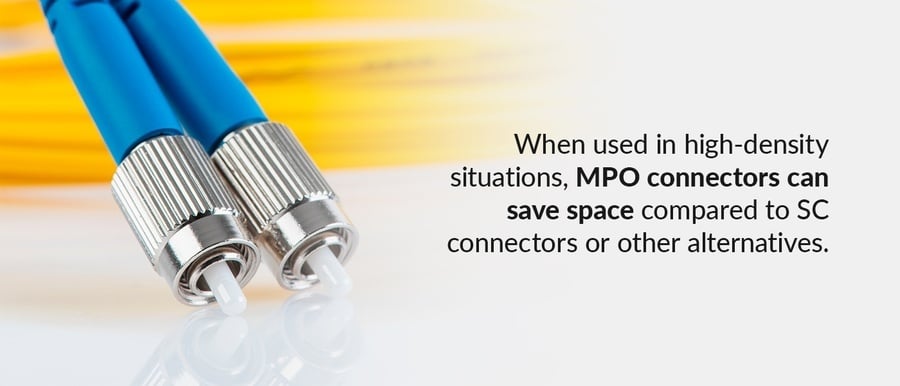
MT-RJ Connector Advantages and Disadvantages
The main disadvantages of MT-RJ connectors
are their rarity and their difficulty for field testing. Adding this
type of termination to a fiber optic cable requires polishing and
splicing, like the requirements for single-mode cables. Consequently,
many technicians choose to use other multimode connectors for fiber
optics that offer easier installation and testing.
Choosing the Right Types of Fiber Connectors
When choosing among different fiber connectors, consulting a fiber optic connector types chart
might help. Knowing the type of cable and the proper connectors for use
with the cable and application help the most. The equipment the
connector plugs into will also play a role in choosing the type to use.
Ask the following questions about a project to choose the right fiber
connector types:
1. Is the Cable Single-Mode or Multimode?
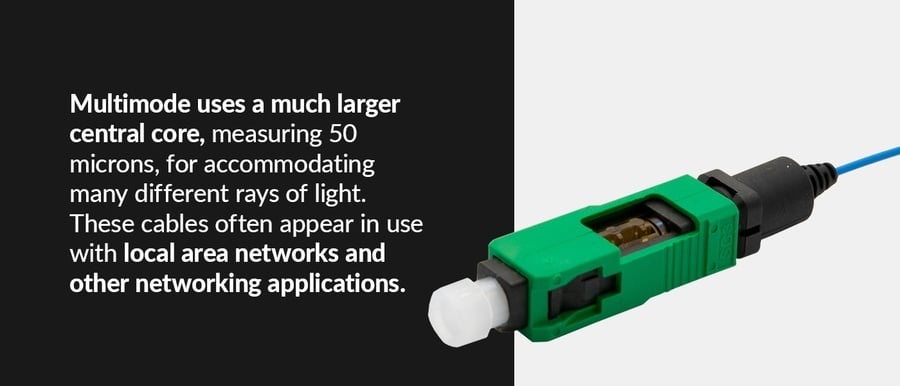
Cables have two main formats, single-mode and multimode.
These modes describe the interior design and the number of rays that
light travels through the fiber in. Single-mode fiber cable uses a
9-micron core through the center that light travels along in one path,
thereby reducing loss and increasing potential bandwidth to 100,000
gigahertz. Both CATV and telephony use single-mode fiber cables.
Multimode uses a much larger central core,
measuring 50 microns, for accommodating many different rays of light.
These cables often appear in use with local area networks and other
networking applications. The type of connector used must work with the
cable design. For instance, SC connectors come in both single-mode and multimode formats.
To identify the type of cable, look at the jacket color. Single-mode cables have yellow or blue covers on the cables.
Multimode fiber cables will be orange, bright green or aqua. Military
applications also use plain green and slate for multimode cables. Since
manufacturers differ in their color choices but remain consistent across
the brand, always check with the cable maker first to verify the colors
used.
Connectors also have colors to designate
their type. Beige typically indicates multimode connectors. Blue is for
ultra-physical contact (UPC) single-mode connections, and green goes
with single-mode angled physical connector (APC) fiber connectors. When
determining whether to use single-mode or multimode, another decision
appears when choosing single-mode connectors — the type of physical
contact.
2. What Is the Type of Physical Contact for Single-Mode Connectors?
The type of connection with single-mode
cables is crucial. Today, single-mode connectors use physical contact
(PC). Some PC connectors have convex ends, which increase the contact
between the cores of the cables. This reduces loss and reflectance,
earning the name of ultra-physical contact.
In some single-mode connectors, angling this physical connection to 8 degrees creates
an angled physical connector, which reduces reflectance even more than
convex PC connectors. This type of connection ensures better
connectivity for use with CATV and similar applications.
3. What Connector Does a Device Require?
Lastly, consider what type of connector the
electronics require. Look at the type of connection required and use
that to inform a decision on the type of terminations needed for the
fiber optic cables leading to the device.